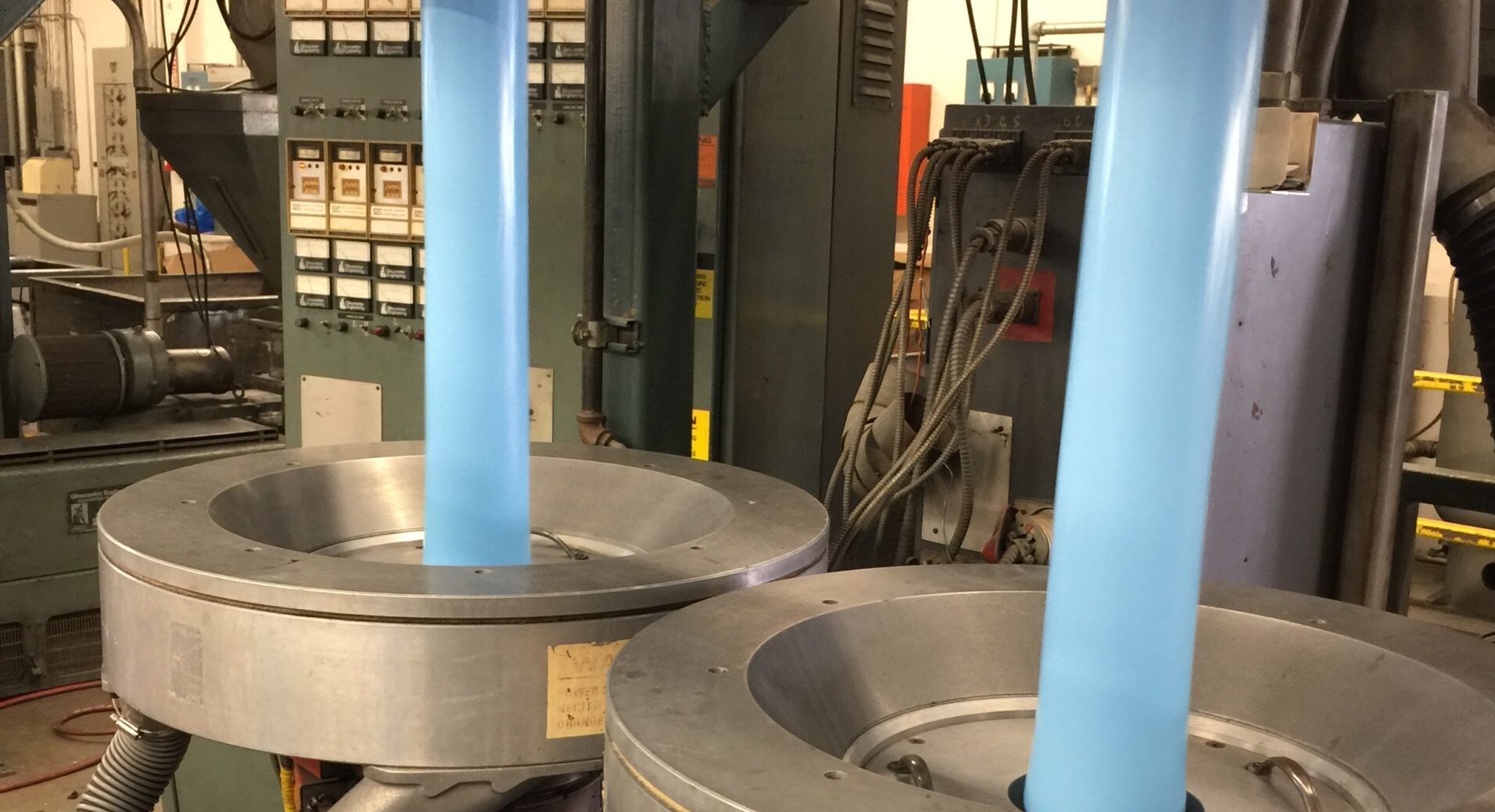
Without doubt, polyethylene blown-film extrusion is widely used in the plastic manufacturing industry for bag production and other packaging products.
As an extruder, TDI Custom Packaging is an expert in the manufacture of made-to-order poly film items and furthermore, has been in business since 1974.
Following is a simple, step-by-step explanation of how the process works:
The Process of Blown-Film Extrusion
1. Raw Material
Firstly, the process begins with polyethylene resin pellets, which are, essentially, raw materials. The resin types can be high-density polyethylene (HDPE), low-density polyethylene (LDPE), or linear low-density polyethylene (LLDPE), depending on the desired properties of the final film.
Brittanica: “Polyethylene Chemical Compound” – read more >>
2. Feeding and Melting
Next, the pellets go into a hopper and then into an extruder. In short, the extruder is a long, heated barrel with a rotating screw inside.
While the screw rotates, it feeds the pellets through the barrel, where they gradually melt and continue moving forward.
3. Blown-Film Extrusion through the Die
After that, the molten polyethylene goes through a die, which is a metal tool that shapes it into a thin tube. This die has a circular opening, and as the molten mass exits the die, it forms a tube of plastic.
4. Inflation
Thereafter, air blows into the extended tube from the center of the die, inflating it into a larger bubble.
Ultimately, it’s the size of the bubble that determines the width. In addition, it’s the speed at which the film pulls through and the rate of extrusion that control the thickness of the film.
5. Cooling
As the bubble rises, air rings blow cool air around the bubble that solidifies the polyethylene material creating a solid film.
The right cooling rate and uniformity are crucial for maintaining the film’s quality and consistency.
6. Flattening
Next, the inflated bubble collapses by passing it through a set of nip rolls. These rolls flatten the bubble into a double-layered film, often referred to as the “layflat” tube.
7. Winding
Then, the layflat film winds onto large rolls. In its final stage, this rolled film is further processed into numerous flexible packaging products.
Custom Blown-Film Extrusion at TDI
TDI Custom Packaging specializes in producing one-of-a-kind poly bags, lay-flat tubing, and sheeting for various industries and applications.
By using the technique of blown-film extrusion, we deliver high-quality film in various thicknesses and widths, tailored to your specific needs.
Please contact our dedicated sales team today for your flexible packaging solution >>
Free Quote